
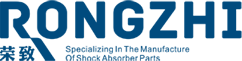
1 rubber Rubber shock absorber rubber material of preparation with ordinary rubber product sizing material, first of rubber were fully plasticating, to have the appropriate degree of plasticity and evenness. With the increase of the plastic refining time, the rubber loss coefficient decreases, and the dependence of the amplitude is reduced. The key of mixing is to disperse the mixture evenly. If the rubber material mixing uneven, will cause the shock absorber stiffness fluctuations, in the rubber due to uneven hardness of the internal stress concentration, thereby reducing the life of the shock absorber. 2 pieces of metal surface treatment and adhesion The vast majority of rubber shock absorbers contain metal parts, and the metal part of the rubber shock absorber must be treated on the surface before it is combined with the rubber, otherwise it will affect the strength of the combination. The metal surface treatment method is more, is the most commonly used in sandblasting, followed by solvent wash, dry glue. At present, the most commonly used adhesive is muruk (CHEMLOK), the adhesion strength is very strong. 3 vulcanization Rubber shock absorber of the commonly used curing method for molding vulcanization, shift molding method curing and injection of three kinds of curing. The most common molding and curing process and equipment are relatively simple, heat transfer from the upper and lower two pressure surface to metal mold and rubber, this method is particularly applicable to large thick wall products. The moving mould method is used for curing the rubber into the metal mould cavity by the pressure of the press, and the forming efficiency is high. Rubber injection mold cavity through the injection hole. Due to the effect of friction, the rubber temperature is improved. In addition, before the injection of rubber and after preheating. Therefore, the shift mode method can shorten the curing time. Complex shape of rubber damping products by injection vulcanization. Rong induced shock absorber rubber stamping pieces called due to injection molding machine injection part and a heating pressurizing part is a whole, rubber sheet or band into the column sene, after fully preheated after high pressure injection metal mold cavity. Curing time should be strictly controlled curing time and temperature. In general, the degree of crosslinking of rubber increases with the increase of the time, the rubber modulus increases, and the loss coefficient of rubber decreases. So, the vulcanized rubber shock absorber to the full, if less sulfur and total sulfur will make the product performance decline. |
Back |