
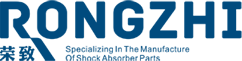
On the one hand, the components of welding deformation, there are strict requirements, also due to the combination of welding cavity near the weld assembly with rubber seals. Therefore, on the welding process of component temperature have strict limits, the welding process has special difficulties. Spatter and deformation by reasonable selection of the type of joint control of welding process parameters of control, and strictly control the technology of component temperature rise lack experience and, therefore, the welding process component temperature strictly control becomes the key to the components can be assembled, will focus on experiments and explorations. Preferably 1 workpiece temperature measurement method Preferably 1.1 temperature measurement method BC 200 a 100 years, ancient Greek Filon and seron their manufacturing a to air expansion for the principle of temperature measurement device. Thereafter, the development of temperature measurement technology of mixed variety. The commonly used measurement method of classification and characteristics of table (2). From the table, compared to the visible, due to the temperature in the vacuum state, through expansion method, pressure method, resistance method, heat radiation method has its limitations. The K type thermocouple for temperature measurement, has the advantages of good linearity, fast response, high precision, the measurement range is wide, and appropriate control of records, moderate price, especially field is simple in implementation, operation and strong. Therefore, we selected K type thermocouple in electron beam welding process the workpiece temperature. (2) the commonly used measurement method of classification and characteristics The implementation of the 1.2 temperature measurement method Since the measurement of workpiece temperature required, therefore, first needs to solve the connection problem of thermocouple and workpiece. In the process, we use the capacitor energy storage welding thermocouple will be welded to the specified temperature by capacitor discharge welding parts, metal foil strip fixed thermocouple compensation wire. The compensation wire connected to the vacuum electron beam welding machine for terminal. In the vacuum chamber the corresponding external terminals through compensation wire connected to DR020R type digital temperature itinerant detecting instrument, the use of the recorder can realize the welding process of the workpiece temperature automatic measurement, display, monitoring and recording. You can also read and print the measured thermocouple welding process of workpiece temperature. Need to be paid attention to in practical welding is vacuum chamber connected thermocouple compensation wire should be around the work twice, reservation and leave the appropriate margin amount after connected to the vacuum electron beam welder terminals, to prevent the welding process due to the rotation of the workpiece, breaking the thermocouple, which affect the measurement and welding normal work of. Control the temperature of the workpiece 2 when the vacuum electron beam welding Control practice by radiating tooling and preferably by welding parameters to achieve the workpiece temperature rise. Using a pair of thick about 30 mm semi cylindrical copper heat dissipation block, and hydraulic cylinder is tightly attached to the surface, auxiliary heat dissipation effect. First of all, experiments were carried out through simulation, to optimize the welding parameters are as follows: Acceleration voltage: 150KV Welding current: 7.5mA Focusing current: 2088mA Welding speed: 20 mm /s After welding, the analog parts are visually, X light, fluorescent inspection, no defects such as penetration, crack, air hole and so on. At the same time as the metallographic examination, the negative form is good, no splash. Actual measurement results: in 20 mm from the weld center near the joint temperature rise is 62 DEG C, the workpiece temperature rise control effectively meet the design requirements. On the basis of the experiment, we have carried out the welding of the actual components. Completed a total of hundreds of pieces of assembly welding, no waste and after welding the elliptic cylinder is less than 0.005 mm, geometric size meet the design requirements. |
Back |